Power electronics technology is advancing continuously. However, this also results in new requirements. The insulation systems of rotating machines, transformers, cables, or bearings experience significantly higher stress due to the steep du/dt voltage pulses generated by the inverter.
In particular, the rapid progress in fast-switching devices presents new challenges that must be addressed by insulation material manufacturers and system integrators.
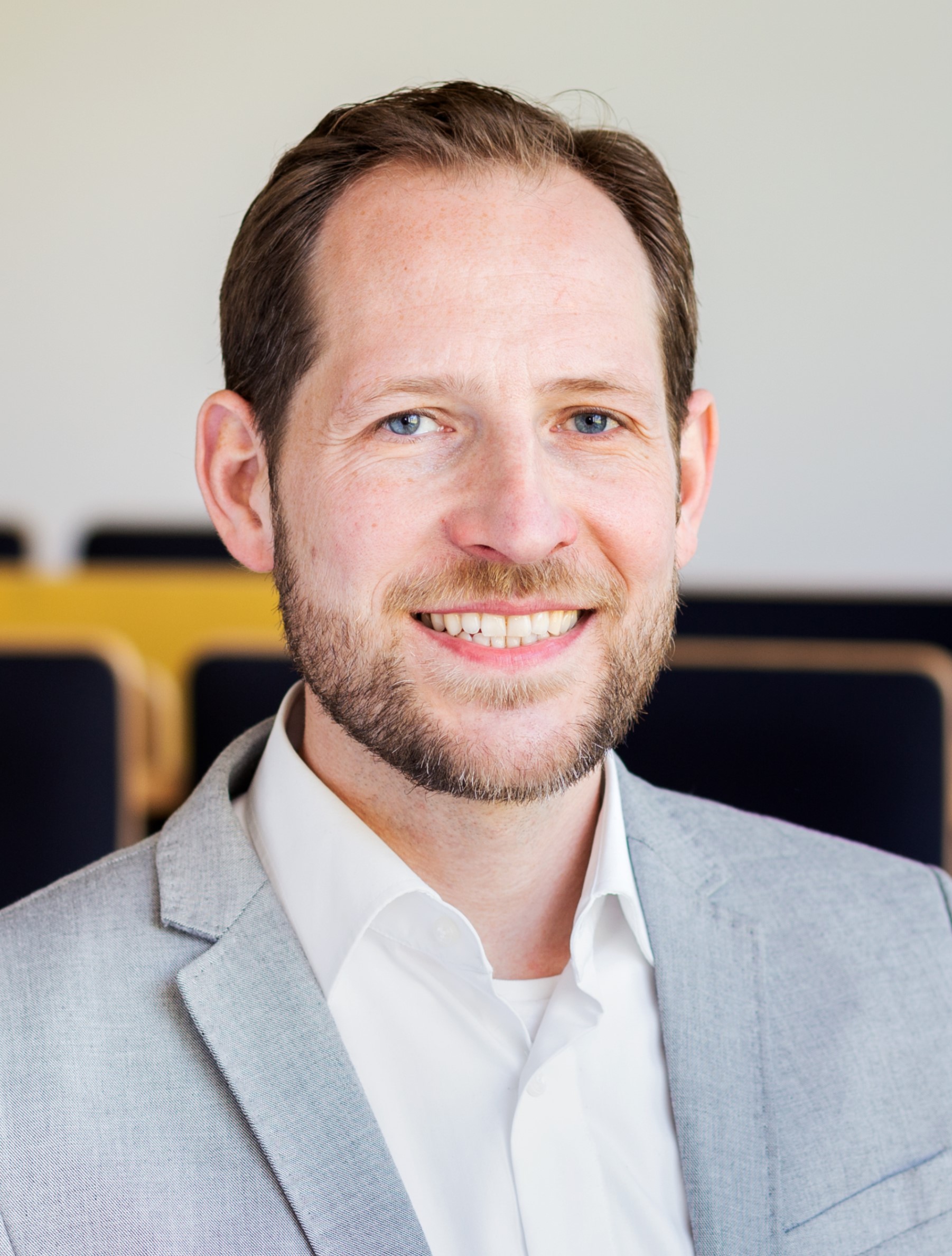
Prof. Dr. Benjamin Sahan — Hannover University of Applied Sciences
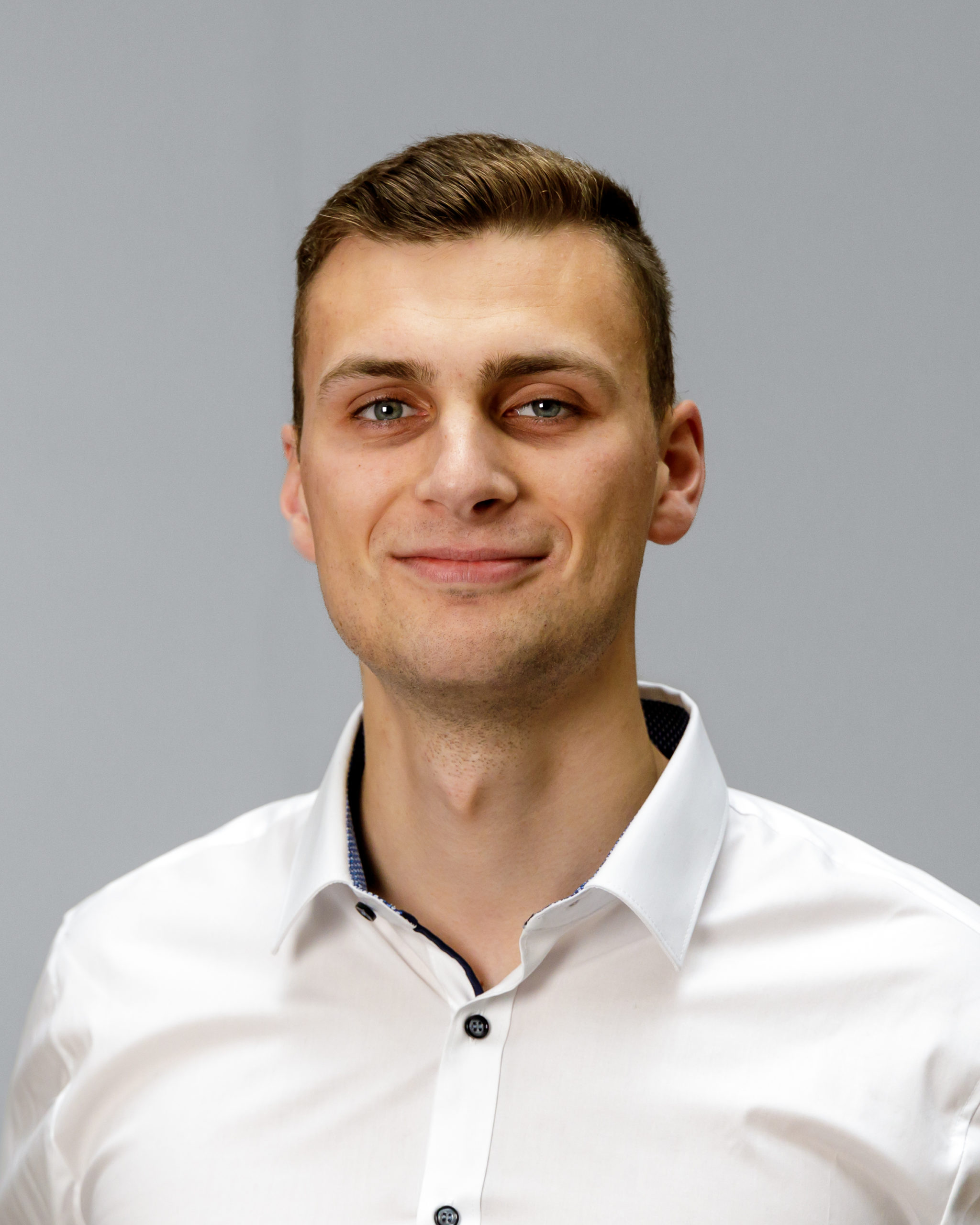
M.Sc. Philipp Berkemeier — SAXOGY POWER ELECTRONICS GmbH
Prof. Dr. Benjamin Sahan (Hannover University of Applied Sciences)
Prof. Dr.-Ing. Christian Staubach (Hannover University of Applied Sciences)
B. Eng. Kevin Kaczmarek (Hannover University of Applied Sciences)
B. Eng. Stefan Reddig (Hannover University of Applied Sciences)
Dipl. Ing. Konrad Domes (SAXOGY POWER ELECTRONICS GmbH)
M.Sc. Philipp Berkemeier (SAXOGY POWER ELECTRONICS GmbH)
M.Sc. Felix Schönlebe (SAXOGY POWER ELECTRONICS GmbH)
This trend is further amplified by the increasing system voltage in many applications, as observed in electric vehicles (400 ➜ 800V) and PV systems (1000 ➜ 1500 V). The application of steep inverter dv/dt slopes leads to increased stress compared to the traditional 50 Hz sinusoidal voltage for some of the following reasons:
- Reduced partial discharge inception voltage (PDIV) and increased partial discharge activity
- Inhomogeneous voltage distribution within the windings [1]
- Polarization effects and dielectric heating due to displacement currents
Figure 1a. illustrates a twisted wire test specimen undergoing stress during inverter operation. Strong corona discharge activity is clearly visible to the naked eye.
In Figure 1c, a conventional enamel wire insulation, also configured as a twisted pair, underwent testing with pulsed voltages, revealing distinct indications of partial discharge erosion.
Lastly, Figure 1b shows an example of a destroyed motor as a result of failed insulation.
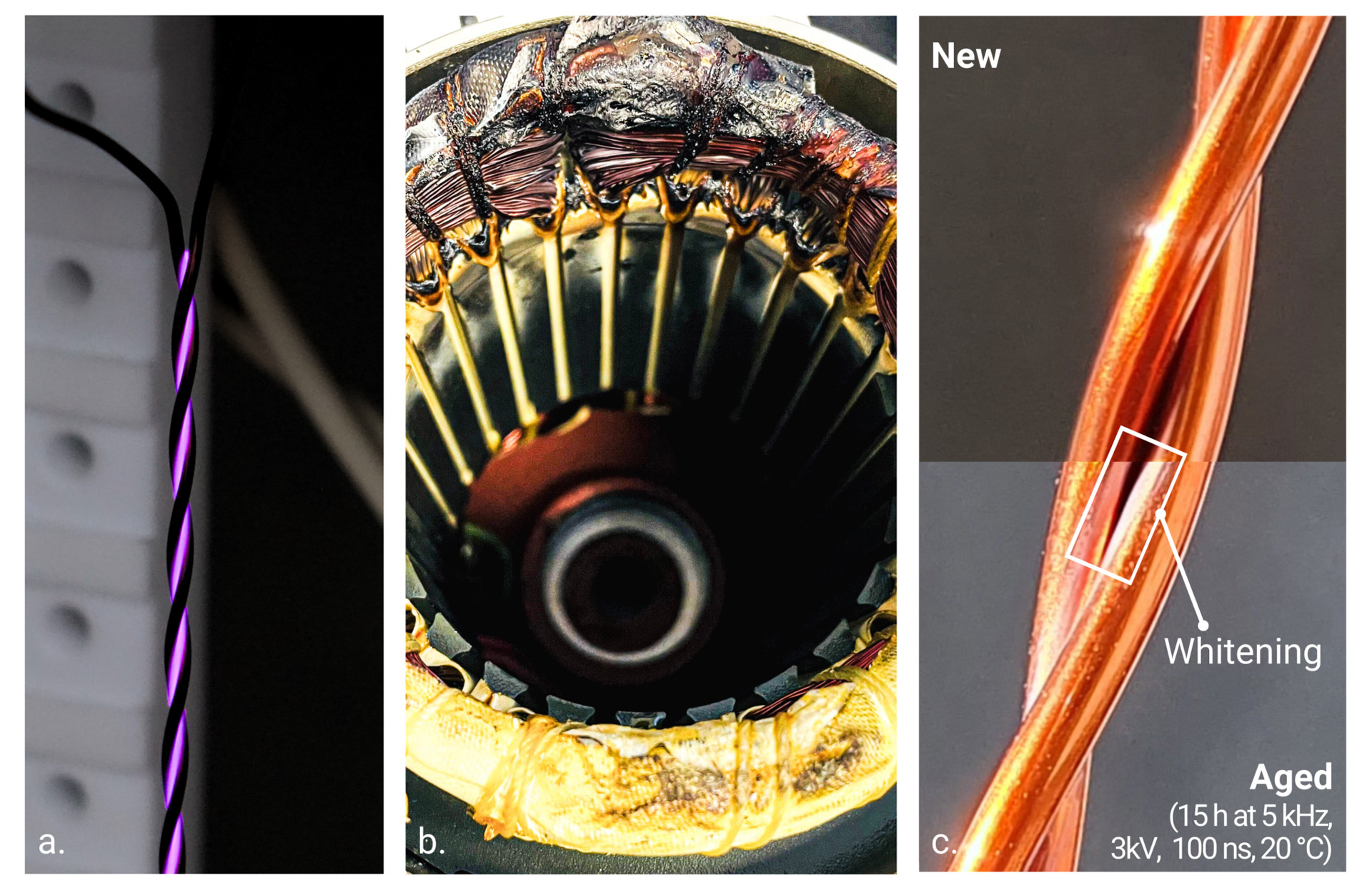
Under these challenging operating conditions, precise knowledge of the aging process and the ability to estimate the remaining lifespan of the insulation system are crucial.
SAXOGY® and Hannover University of Applied Sciences have taken on the task of developing a test bench that realistically simulates the stresses of inverter operation and can be used for accelerated insulation endurance assessment. The corresponding project “ISODyn” was supported by the German ZIM research funding.
Which requirements are used for testing?
Currently, there is no unified international standard for endurance testing under high-frequency voltage impulses for winding wires. Therefore, we refer to the existing chinese standard GB/T 4074.21-2018 and incorporate feedback from manufacturers to derive the following requirements according to figure 2 that the dv/dt pulse generator must meet.
- Voltage waveform: Bipolar square wave
- Peak voltage: 1,5 kV (should be modular extendable)
- Rise time tr > 25 ns (10-90%) – adjustable
- Max. voltage slope dv/dt: 60 kV/μs
- Pulse frequency: 20 kHz
- Test temperature >180 °C
- Voltage overshoot (1-Up/Ua) < 2%
- Grounding of the device under test
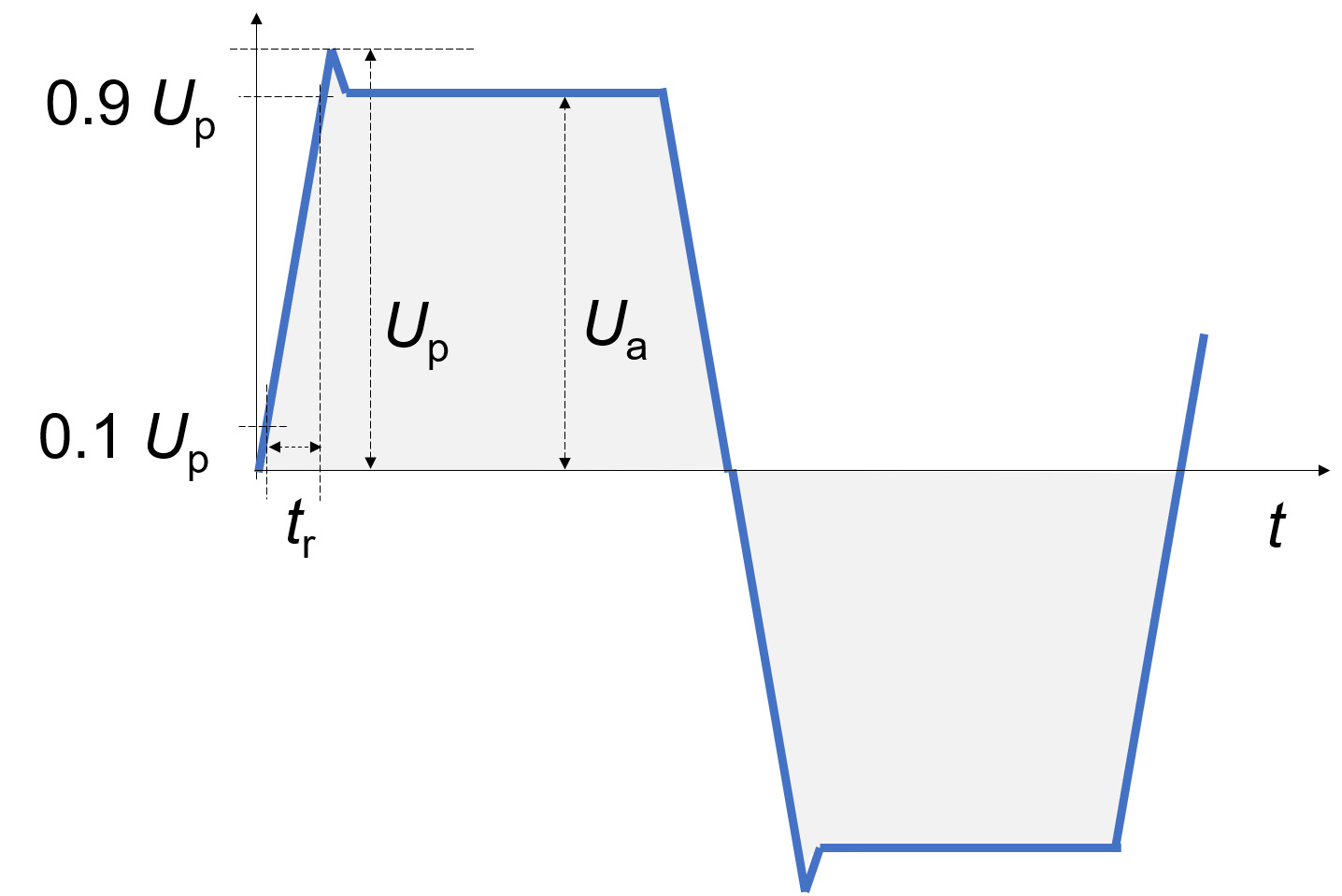
The breakdown of motor windings due to insulation failure occurs when the insulation degrades over time under the influence
of steep dv/dt voltage pulses. This degradation can lead to arcing, ultimately reducing the insulation resistance and resulting in a breakdown. Reliable detection of this breakdown is necessary to prevent damage to the test bench and accurately define the resulting lifetime.
Factors influencing insulation lifetime
Various measurements are carried out in endurance tests. The ensuing results were subjected to statistical analysis. The test samples consists of twisted pair copper wires that met the specifications of the IEC 60851 standard.
First, the influence of the pulse frequency fp on the resulting electric lifetime of conventional copper wire enamels without additives is investigated (see Figure 3). The samples failed after about 4 min (for 11 kHz) to about 55 min (for 1 kHz) in average. It can be summarized as follows:
- the electric lifetime decreases almost lineary with increasing frequency fp
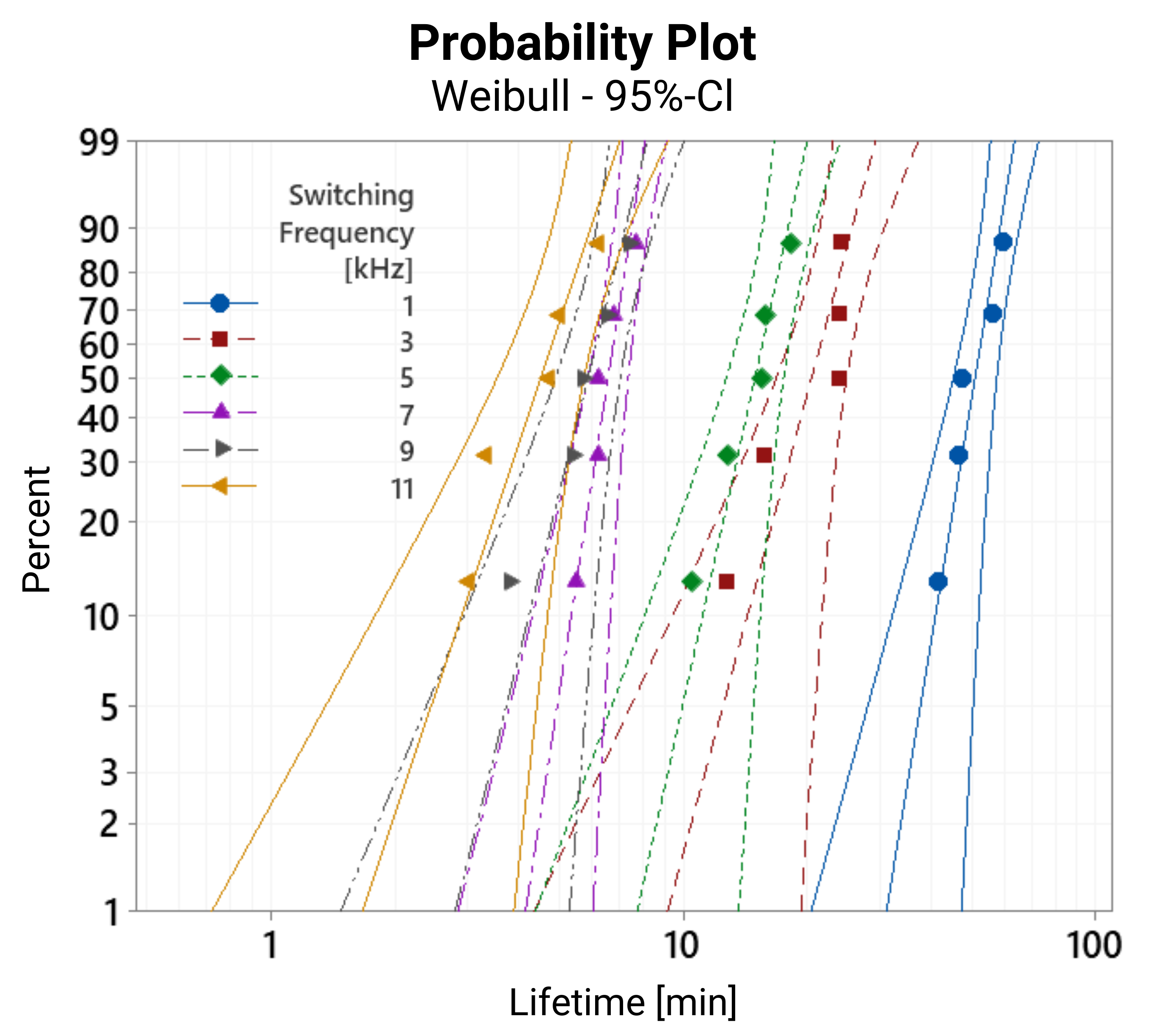
Additionally, the effects of slew rate, temperature, and insulation material on the resulting lifetime has been investigated, examining different combinations of rise time (tr) and oven temperatures [2].
- variations in rise time have a noticeable impact on lifetime (see Figure 4)
- increasing the temperature reduces the electric lifespan (see Figure 4)
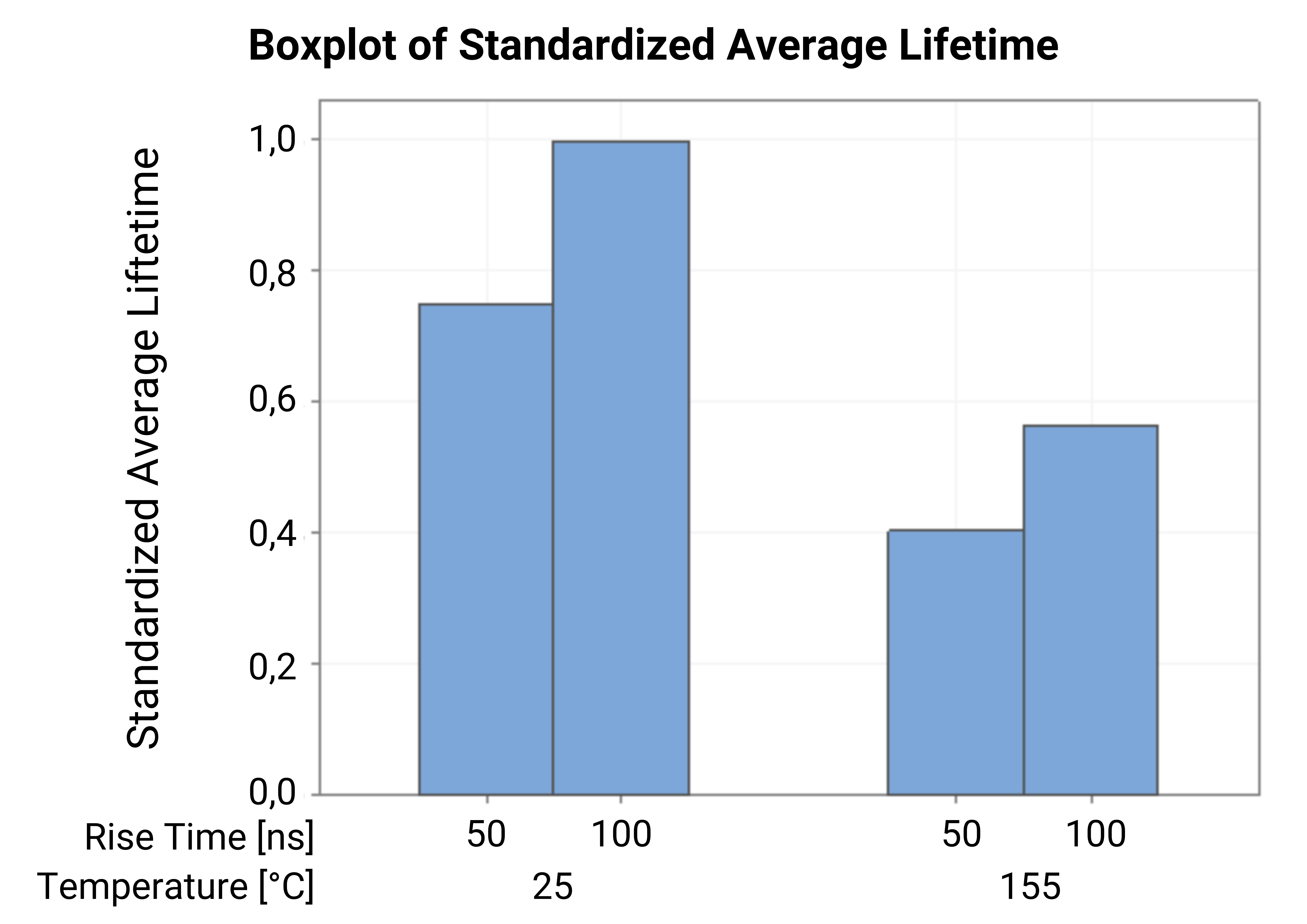
Furthermore, the choice of insulation material and its structural composition were found to significantly influence the overall lifetime [2].
Unique modular dv/dt pulse generator test bench for lifetime testing
SAXOGY POWER ELECTRONICS and Hannover University of Applied Sciences have jointly developed a modular high-voltage pulse generator, as shown in figure 5.
This generator consists of state-of-the-art SiC MOSFET technology. It is designed to be adaptable allowing for expansion to fulfill the specific test requirements for lifetime testing and upcoming standards in terms of insulation testing.
The concept is scalable and can be expanded to meet specific application needs. The bipolar voltage waveform is adjustable across a broad voltage range, from 0,4 kVpp to 12 kVpp, depending on the configuration and the generator can achieve voltage slopes up to 200 kV/μs.
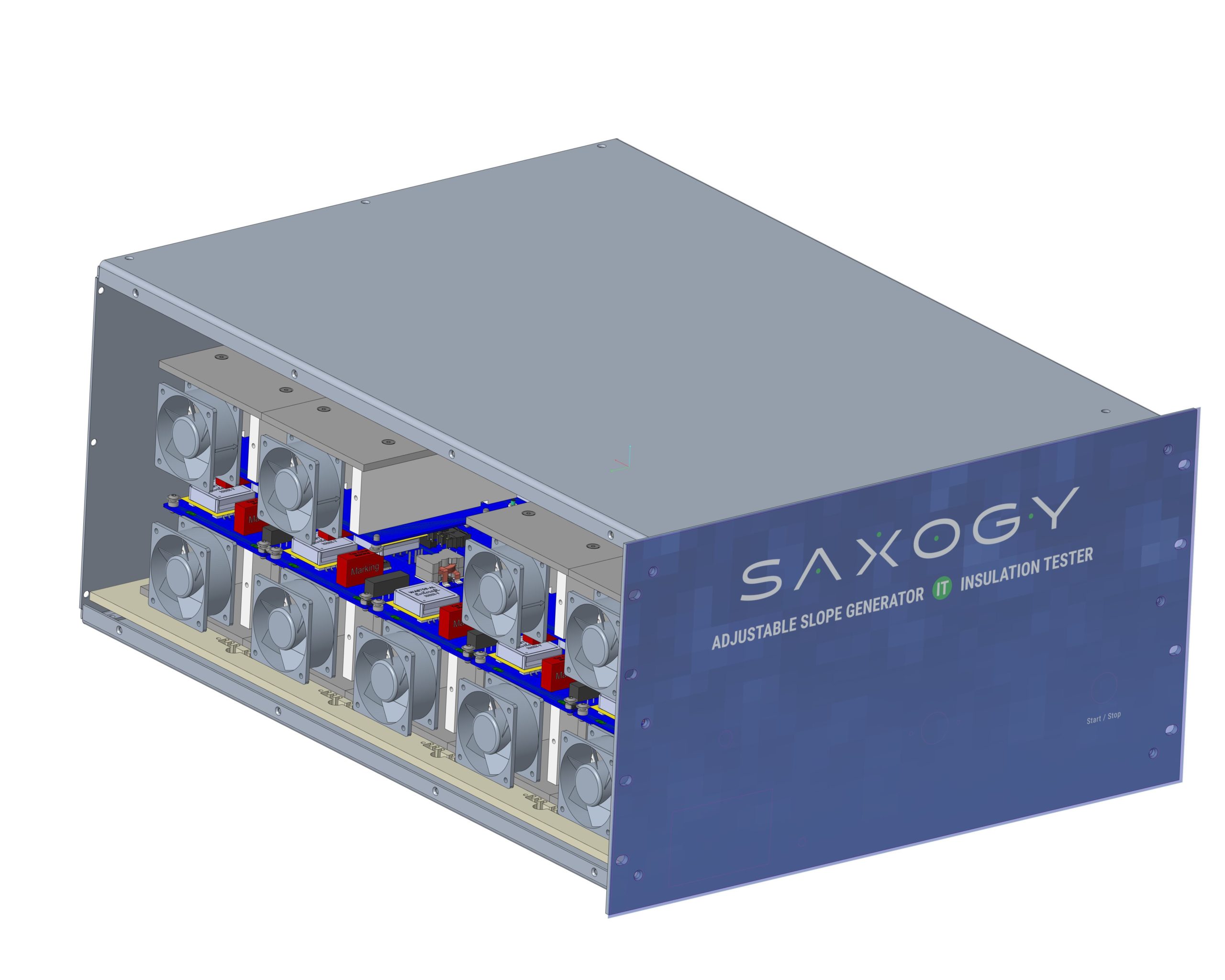
Adjustable load setting
A precise gate driver circuit has been developed to ensure that the overshoot of the SiC inverter remains below 2%.
Furthermore, an almost linear voltage gradient was achieved during the switching time, ensuring a consistent stress in every rising and falling edge. To adjust the stress level, there are 16 steps to fine-tune the voltage slope based on the requirements of the individual insulation testing standard. To vary the test time for accelerated endurance tests, the generators square wave frequency can be set between 2 kHz and 20 kHz.
In addition to the electrical key figures for insulation testing, the development focused on two essential requirements for an insulation endurance test bench:
- the generator must never exceed its own insulation limits and cause stress to itself
- Most insulation tests end with an insulation breakdown, which from the generator’s point of view represents a low impedance short-circuit. This short-circuit current must be detected and handled within microseconds. This process is repeated beyond the device’s lifetime.
Further details regarding the development of the pulse generator and its various configurations will be elaborated upon in part 2 of this article.
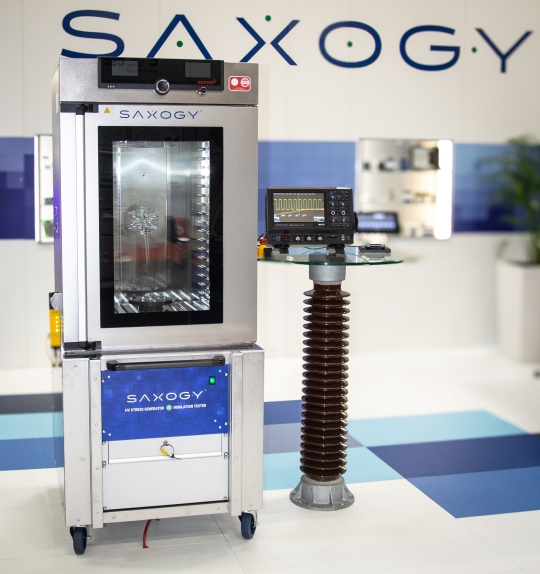
Reaserch and development in accelerated insulation endurance testing
The collaborative effort between SAXOGY® and Hannover University of Applied Sciences has resulted in the development of an advanced modular dv/dt pulse generator. This innovative testbench represents a significant leap forward in accelerated insulation endurance testing. It offers a valuable tool for validating existing and developing new insulation systems, thereby contributing to the enhancement of future power electronic systems.